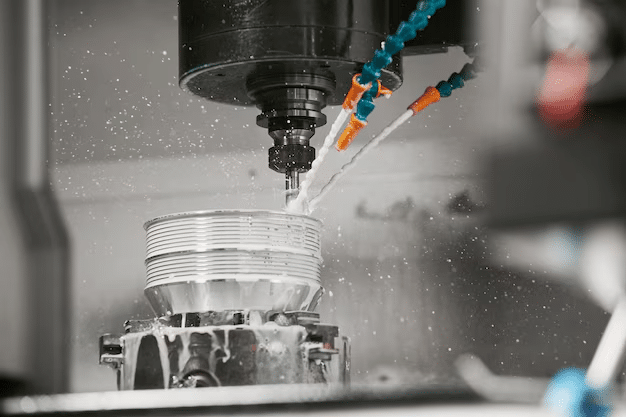
When it comes to machining metal parts, selecting the right coolant can make all the difference. Not only does the proper coolant help manage heat and reduce tool wear, but it also improves surface finish, chip removal, and overall process efficiency. In this post, we’ll explore the various types of metalworking coolants, discuss key factors to consider, and offer some guidance to help you choose the right solution for your operations.
Why Coolant Matters
Coolants help by:
- Managing Heat: Preventing tool wear and workpiece damage.
- Enhancing Lubrication: Reducing friction for smoother cuts.
- Aiding Chip Removal: Keeping operations clean and efficient.
Types of Coolants
Choosing the right coolant often means selecting a formulation that aligns with your machining requirements. Below are the primary categories—with examples from the Durakut line we sell at Emultec Industrial—to help illustrate your options:
Water-Based Coolants
These are typically water-soluble cutting fluids that form emulsions with water, providing excellent cooling and effective chip removal. There are many different products to chose from out there but Falcon Industrial Inc. manufactures two of the undoubtedly best products on the market.
- Durakut 6185: A high-performance, soluble metal removal fluid engineered for versatility in machining a wide variety of materials. It offers outstanding heat dissipation, cleanability, and microbial control.
- Durakut 6195EP: Designed for demanding machining applications, this coolant delivers exceptional lubricity, ultra-low foaming, and superior bio-stability, making it ideal for processing materials like aluminum, steel, and titanium.
Oil-Based Coolants
Oil-based coolants traditionally provide superior lubrication for heavy cutting and high-friction operations. However, the Durakut product line emphasizes water-soluble and synthetic solutions to balance performance with ease of maintenance. As such, none of the Durakut products are pure oil-based formulations.
Synthetic & Semi-Synthetic Fluids
These fluids combine the benefits of water-based cooling with enhanced lubricity—ideal for precision machining.
- Durakut 525: A semi-synthetic cutting and grinding fluid tailored for machining aluminum and ferrous alloys. It offers the boundary lubrication benefits of soluble oil while retaining robust cooling properties, ensuring extended tool life even under high-severity conditions.
- Durakut 4010: A fully synthetic coolant formulated for grinding, sawing, and machining applications. It provides extended coolant life, excellent rust protection, and low foaming, making it especially suited for operations involving ferrous metals.
Key Considerations
Selecting the right coolant isn’t one-size-fits-all. Consider these factors:
- Material: Different metals (e.g., aluminum vs. steel) may require specific coolant properties.
- Machining Process: Turning, milling, or grinding each have unique coolant demands.
- Equipment Compatibility: Ensure your machine’s cooling system is designed for the chosen formulation.
- Maintenance & Cost: Factor in long-term upkeep, disposal, and the overall cost-effectiveness of the coolant.
As much as we wish there was, there unfortunately isn’t a universal answer to which metal working coolant you should use. The best choice depends on your material, machining operation, equipment, and budget. Whether you opt for water-based solutions like Durakut 6185 or Durakut 6195EP, or prefer the synthetic advantages of Durakut 525 and Durakut 4010, assessing your process requirements and testing small-scale applications will guide you to the ideal solution.